
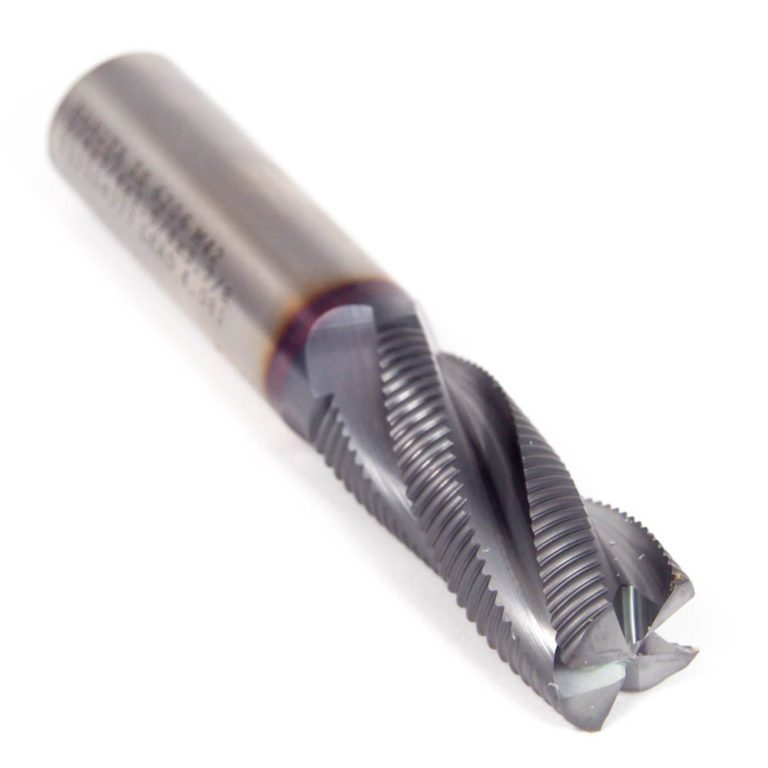
Second, you have taken very good photographs and because of this it is plain to see that that end mill is essentially junk. Are you stuck with using Weldon style holders or is there a collet setup alternative that you could use? I am assuming here that a collet would reduce overhang considerably. Ok, I didn't read all of Arthur's replies so if I duplicate here, sorry.įirst, you are absolutely correct, 5" is way to much overhang. So if you're only feeding in X axis, lock Y axis and Z axis (quill). I should have also mentioned that locking unused axis is a good practice. *collets are good, but I would like to know what your spindle is: R8, MT2, MT3? When you start getting into larger end mills, like 5/8" or 3/4", collets of these types start to become questionable in resisting large cutting forces (depending on who you're listening to ). I think that is what you were getting at with the third paragraph above? *I like to use the longer length of engagement on the edge-not the end-of the end mill if possible. *yeah, 20 - 50 thou' DOC is pretty normal for a machine of that size. I don't know if my verbose reply has anything to do with the original intent of this thread. I expect, though, you will be shocked at how much of a cut, feed, force it takes to achieve these failure modes with a 1/2" HSS end mill. The failure modes are going to basically be *overheating the end mill-it'll turn colors and start to look like a misshapen lump instead of having cutting flutes *break off a sharp corner on one of the flutes, thereby creating a horrible surface finish only good for roughing *overheat the workpiece-then there aren't "chips" because the molten mass welds to the edges of your cutting tool, happens a lot with aluminum The end mill is physically retained by the set screw, and the holder is physically retained by the drawbar. In that respect, those end mill holders such as you are using are extremely safe. See when and how the resulting surface finish and end mill performance relates.īefore all that, though, it sounds like you are building confidence in both toolholding and workholding.
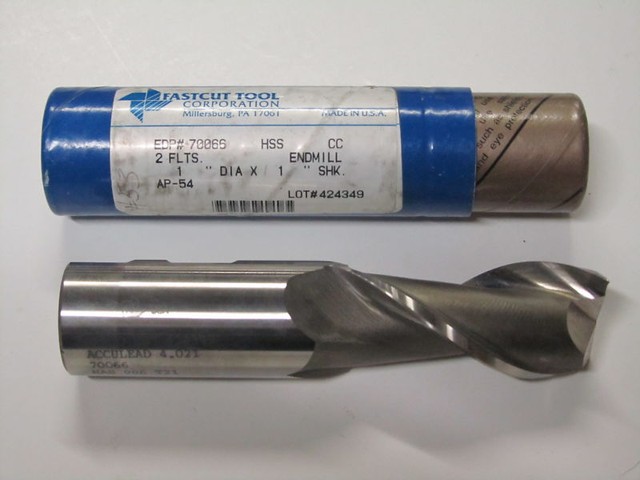
Try deep cuts, shallow cuts and fast cuts.

I'd recommend getting a good size block of steel that is taller than your vise jaws and try burning up an end mill It'll teach you a lot.
#Fastcut end mills review manual
The rest can be picked up by feel on the manual handwheels and learned by experience. So now that it sounds terribly complicated and esoteric, I'll say that SFM and RPM is all that really needs to be referenced and calculated out.
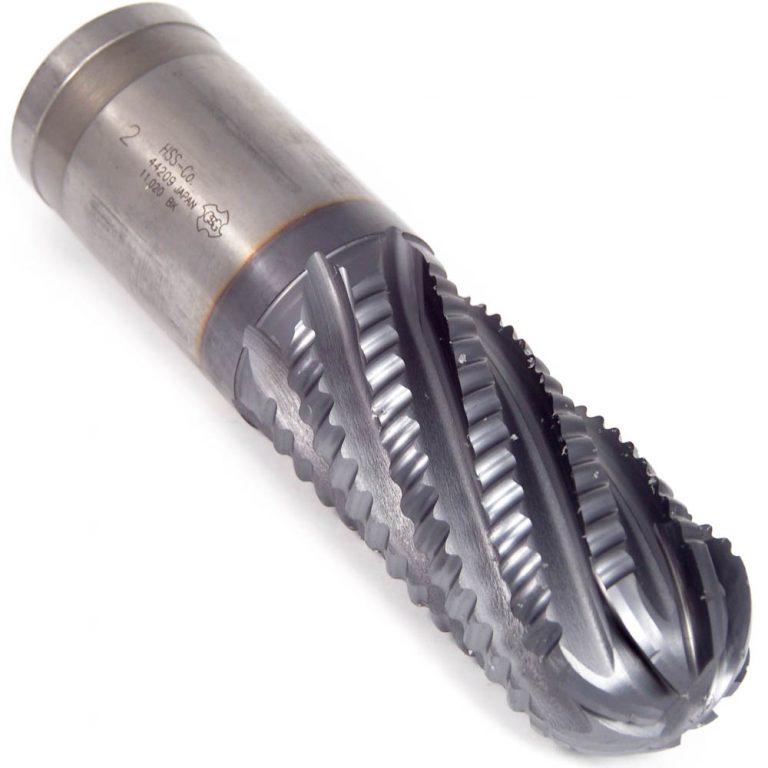
This is called chip load-a similar but different way to measure the "depth" of the cutting action. Varying the spindle rpm with the same feed rate also changes the amount of material each flute digs into to make the actual cut. A deep cut at a slower feed is similar to a lower DOC at a faster feed. There is also a relationship between depth of cut (DOC), feed and speed to be aware of. 312" depth of cut for the simple reason that there isn't much of the workpiece to hold onto in the vise. For that particular piece, I wouldn't take the whole. Your caution is completely understood and not at all a bad thing. They are available from Little Machine Shop for $11 each. Next time I need to do something like this, I'll get a little more bold and up the RPM and feed rate.Īlso, perhaps a collet would get the cutting edge closer to the spindle.
#Fastcut end mills review full
I was also wondering if it was better to set the depth to the full 0.312" and take multiple passes using the Y axis, or shave the full width of 0.312" as I did, and then take cuts at increasing depth, which is whatI did. I don't have a fine vertical feed (Z-axis), so I just loosen the spindle lock slightly, tap it down a bit, and then give it a try. For milling plain carbon steel it's 65-1-1026, and 25-100 for higher grades: Īlso, I had started with a vertical depth of about 0.01 to 0.02, and then worked my way up to 0.020 to 0.050, and the full width of the notch (0.312"). I used the 220 SFM from a chart for turning. I calculated the SFM after the fact, and I've usually just used this low RPM for almost everything. Also, my previous milling experience using the Jacobs chuck rather than a proper mill holder has made me a bit "chicken". I suppose I have always approached machining with a lot of caution, since I have not had the benefit of a mentor showing me what to do.
